The process is quite straightforward, but not without difficulty.
Step 1: Product principle and characteristics
The first thing we need to do is understand the characteristics and principles of optical fiber fabrics- optical fiber fabrics, also known as luminous fabrics, LED luminous fabrics, are a kind of plastic optical fiber used as warps or wefts. The fabric is made up of plastic optical fibers coupled with F5LEDs that are controlled with an electronic system. It emits light and changes color. Basically, it’s a high-tech fabric.
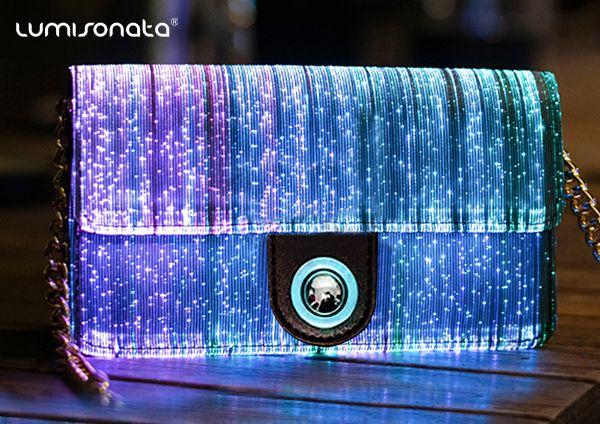
Step 2: Tools Preparing
We should know in advance what products we will use fiber optic fabrics for. Design drawings, tools and materials such as scissors, paintbrushes, utility knives, thread, sewing machines, hot cutters, hot melt guns and hot melting glue are then required as shown in this figure:
Step 3: Tailoring
Draw a picture on the fiber optic fabric according to the design artwork. Then cut it with scissors. Note that fiber filaments in the fiber optic fabric cannot be cut. Below are a few pictures that will help you understand this statement better:
Step 4: Liningistics
Optical fiber fabric is usually sewn together with a cloth after it has been cut. As a result, it makes the light bar line less noticeable.
Step 5: Sewing
Sewing worker needs to perform normal sewing after sewing and pasting the supporting cloth. During the sewing process, the sewing machine’s pressure angle must be adjusted to the lightest so that the fiber is not affected by the sewing process. Ensure that there is no crushing of plastic optical fiber.
Step 6: Bundling the Optical Fiber
At one end of the fiber fabric, the bare fibers are bundled according to a certain span, as shown in the figure:
Step 7: Cutting the Optical Fiber
We use a hot cutter in order to cut the optical fiber bundle when it has been assembled. . A fast, accurate approach is necessary. The cross-section of the cut should be relatively flat.
Step 8: Coupling the LED Lights
After the fibre bundle has been flattened, it needs to be butt-coupled to the F5LED lamp bead. Heat shrinkable tubing is generally used for this type of connection. Shenzhen Fashion Lighting Technology Co., Ltd. does an excellent job in this regard. LED lights are their specialty. Their molds are open on both sides of the beads and fiber bundle, and they can be tightened by aligning the threads. I really like the convenience and quality of their products.
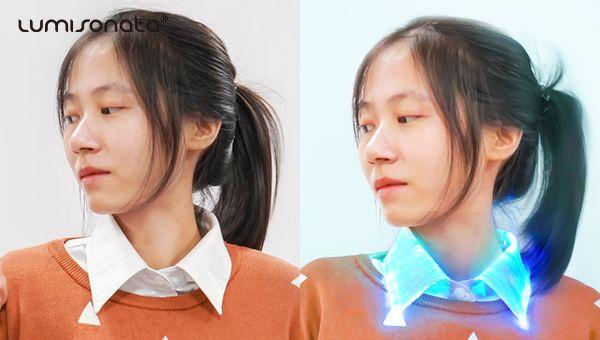
Step 9: Seam
Once you’ve finished the above steps, turn it over and press the seam.
Step 10: Quality Inspection
In order to comply with optometry inspection quality requirements, the following factors need to be met:
a) Wide and uniform sewing lines are essential, as well as fine and wireless sewing heads.
b) There should be no continuous breakage of fibers. Fibers that are broken by more than 1CM are considered unqualified.
c) The product must be clean, tidy, and in strict conformance with the production specifications.
d) The product must possess a uniform and translucent luminescence.
Step 11: Packaging
Because most fabrics cannot be folded 180 degrees, which will damage the fibers that guide light, packaging should include foam sticks. Folding prevents damage to the optical fiber. The following pictures illustrate this:
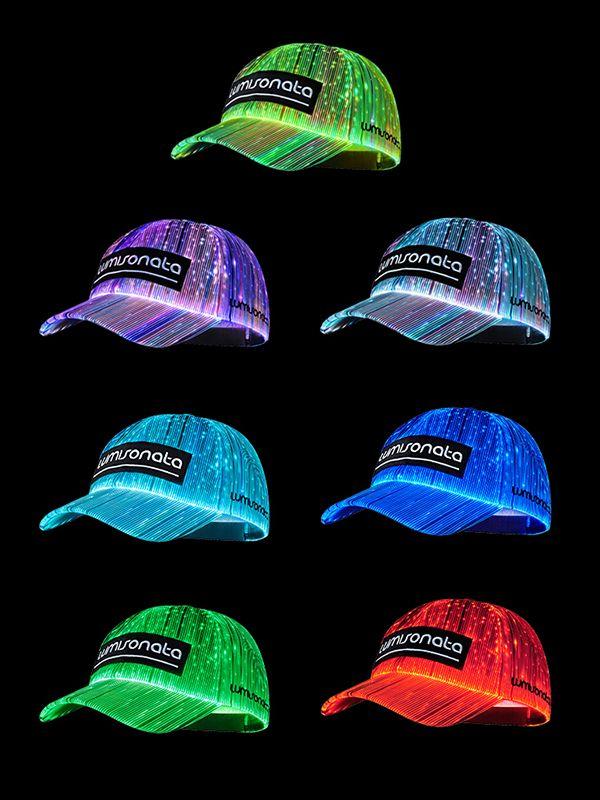
To Sum Up
Pls give us your comments
In this way, a fiber fabric product is created using luminous optical fibers. You are welcome to contribute your knowledge and experience regarding fiber optic fabrics by commenting below.